Capacity Partners with Lightning Pick for Improved Fulfillment Productivity
Back to Blog
When our clients face a challenge, the culture at Capacity demands that we help them find a lasting solution. So what happens when the challenge occurs internally, within our own walls? Thankfully, there is no shortage of innovation in the e-commerce fulfillment sector, so we have plenty of places to turn when a new solution is needed. That's why, when faced with the challenge of increasing accuracy rates for a growing e-commerce client base, we turned to the Lightning Pick 'Pick-to-Light Cart / Put-to-Light' system. By replacing a more manual pick system with one that tells the user exactly what they need and where to put it, fulfillment productivity is immediately increased. The Put-to-Light solution is tailored for our team to focus only on the core task of getting the right product in the right place "We really don't want someone who is putting 1,200 units in an hour to be focusing on anything else," says Capacity CEO Jeff Kaiden. Likening the system to a video game, he explains that productivity and accuracy are vastly improved as team members get into the rhythm of the system. With its scanner-based verification, automated put light indicators, and clear quantity displays, the system cuts down on training time and reduces the number of checks required to ensure order accuracy. "Accuracy is so good, we have all but eliminated error rates on e-commerce orders filled through the system," says Thom Campbell, Chief Strategy Officer at Capacity. With thousands of orders moving through these put walls every hour, the impact on productivity is enormous.
In terms of productivity, Capacity is already reaping the rewards of partnering with Lightning Pick. Consider the following data points, summarized after just a few months of operation:
Productivity Improvements
The video below provides a step-by-step look at how the system works.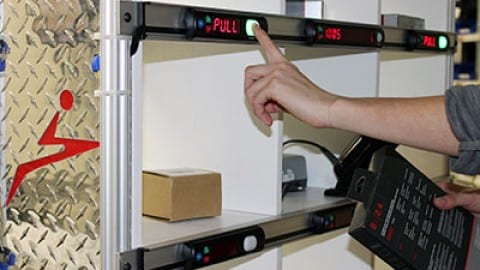
- For high volume clients, maximum daily throughput is more than led since the introduction of Lightning Pick.
- The scan system reduces the need for an extra person on quality control, as the previous paper pick system required. Error rates, which were already less than 1%, are now so low that they can be considered negligible.
- Across a full day and night shift, order processing capacity has been increased to 12,000 units. Before the new system, this would have been capped at around 2,500 orders.